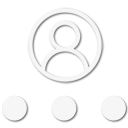
Member III
Member III
Traveler II
Traveler II
Advocate I
Traveler II
Traveler II
Traveler II
Traveler II
Traveler II
Traveler II
Traveler II
Traveler II
Traveler II
Member III
Traveler II
If you squint, there is still some yellow over spray on the safety chains that I reused. It is such a relief that the yellow is gone!There ain't much yeller left in Project Yeller! You could always paint the doors yellow. What about the Turbines?![]()
You are absolutely right. The narrow frame and narrow suspension isn't ideal. I suspect the higher capacity leaf springs will help keep the trailer stabile with the extra leverage created from the spring to hub distance on the axle. My only fear is that the extra leverage could bend the axle, so I am keeping a close eye on it.Glad you upgraded the axle, and the trailer looks pretty light but the narrow frame creates a lot of leverage from the spring to the hub...
Be diligent monitoring the axle.
Traveler II
Traveler II
Traveler II
Member II
30139