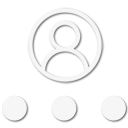
Member III
- 2,827
- First Name
- Tom
- Last Name
- Houston
- Member #
-
8300
- Ham/GMRS Callsign
- WØNUT Extra
I am a blue tape and cardboard mockup guy.Drawing it out doesn't cut it for me. The concept picture is almost scaled correctly and I still didn't know how it would be when it was done.
I taped the opening to what was a standard door size and I would catch my shoulder, head and tear the tape. Then once inside, I realized I didn't like the window size and placement. Got the size set and they were sold out of what I wanted. Found another size and did the tape again. My rear cabinets and doors were the same.
A tip: find a local business that specializes in building shipping containers and packing for industries. They will have very large single sheets of cardboard that you can cut and tape to build a proto before spending big bucks on materials and having to scrap them.
Sometimes I actually get sheets of .125 Masonite for the same purpose.