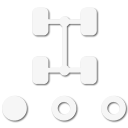
Off-Road Ranger I
I very nearly made that mistake with the coolers when I swapped to a vertical-filter adapter plate. Ended up going with the same 5-fin cooler instead of the bigger 7-fin from the six cylinder engines.Hey Tinker--you may already know this, but make sure the oil cooler is from a 4BT, as 6BT's and 4BT's are ported different, so you starve some galley's if you swap them. We did a Range Rover 4BT. ended up using a P38 steering box outboard of the frame to clear the front cover. Cool conversion when it's done though. Used a Diesel Conversions 4500 to t-case adapter to shorten the package--that dang shift is really close to the dash. Cool rig man, I'm anxious to see that thing up and running!!!
I'll have to look into the P38 steering too, thanks for the heads up!
Yeah that shift tower on the NV just doesn't wanna line up where I want it... might end up slicing the shifter off at the base & weld a dogleg into it like this to fit under the dash:
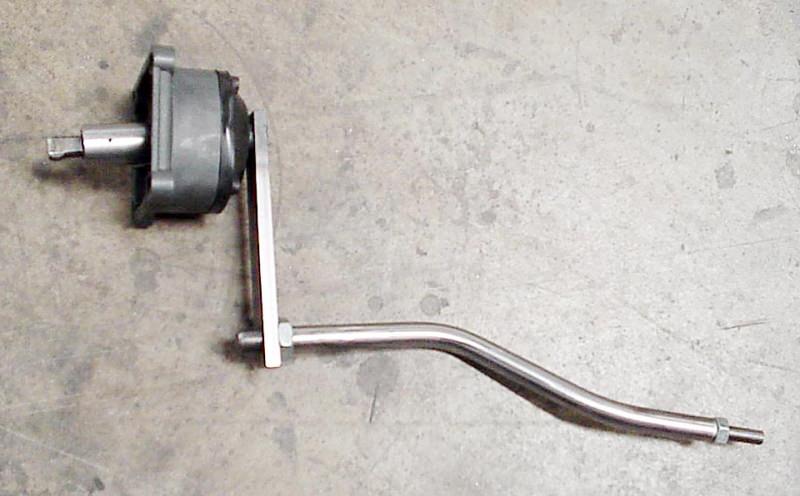