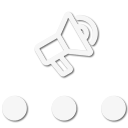
Enthusiast III
I've been wanting a teardrop trailer for several years - probably almost 10. Several times I've sketched out ideas for a teardrop, a square drop, or a weekender style trailer. Last spring I picked up a trailer and built a canoe rack and used it to carry camping tubs for the season. It worked great, but it was seriously lacking. We were still camping primarily in a tent, everything had to be pulled out of tubs, setup, and then repacked when we were done. It worked well for weekend trips that were mainly focused on a canoe/kayak trip. It wasn't so great for more overloading/longer-term travel/camping. Last fall I spent a week at a few different camp locations in the high country of Colorado and the experience confirmed I needed a better setup. During all this time I'd been chatting with my friend Jeff who had built a teardrop for himself and later took that experience to start Hyk Outdoors.
Hyk was building 5x8 teardrops in both on and off-road versions as well as offering kits you could build yourself. My family checked one out for a weekend and my wife was sold as well. The ability to grab clothes, food, and a few other items tossed into a trailer and be on the road to camp was well worth it. Our weekend with the trailer confirmed two things though - we're both tall and wanted a longer bed, and we wanted a galley that minimized the amount of work to setup and cook. I also knew we wanted an their off-road trailer, a fridge in the tongue box, and a full roof rack to carry a boat or two. After a few conversations we started sketching out plans for a 5x10 trailer, using the extra two feet to extend the galley and add an 80" bed. The plan was to work with their team on a kit that provided exactly what we needed.
We're just now wrapping up the build and I've got to say the experience working with Jeff, Mark, and Caleb has been outstanding. These guys do great work and have helped me make decisions about the trailer given their experience and provided guidance while building it. I'm going to be posting through this thread photos and the process of building. I'm really glad I worked with the Hyk team rather than trying to build something from scratch on my own.
Here's a look at their 5x8 off-road trailer. These things are bad ass and have amazing attention to detail. Other than this initial photo, the rest of the thread will be the Blue Whale - what they've apparently named our teardrop in the shop. When everything is all said and done I'll add my completed trailer here as well.
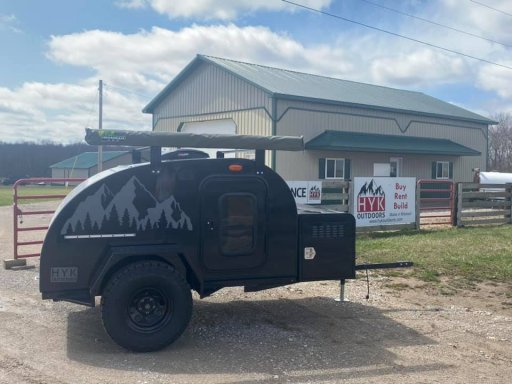
Hyk was building 5x8 teardrops in both on and off-road versions as well as offering kits you could build yourself. My family checked one out for a weekend and my wife was sold as well. The ability to grab clothes, food, and a few other items tossed into a trailer and be on the road to camp was well worth it. Our weekend with the trailer confirmed two things though - we're both tall and wanted a longer bed, and we wanted a galley that minimized the amount of work to setup and cook. I also knew we wanted an their off-road trailer, a fridge in the tongue box, and a full roof rack to carry a boat or two. After a few conversations we started sketching out plans for a 5x10 trailer, using the extra two feet to extend the galley and add an 80" bed. The plan was to work with their team on a kit that provided exactly what we needed.
We're just now wrapping up the build and I've got to say the experience working with Jeff, Mark, and Caleb has been outstanding. These guys do great work and have helped me make decisions about the trailer given their experience and provided guidance while building it. I'm going to be posting through this thread photos and the process of building. I'm really glad I worked with the Hyk team rather than trying to build something from scratch on my own.
Here's a look at their 5x8 off-road trailer. These things are bad ass and have amazing attention to detail. Other than this initial photo, the rest of the thread will be the Blue Whale - what they've apparently named our teardrop in the shop. When everything is all said and done I'll add my completed trailer here as well.
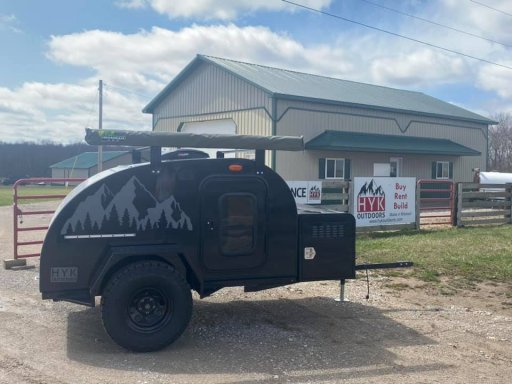