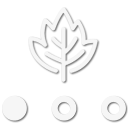
Steward I
Ok, let's discuss my plan and you all can pick it apart or offer suggestions! You are going to have to use your fabrication imagination here, LOL.
First, the vehicle: 2014 Jeep JK Unlimited (the 4 door for the non-Jeep crowd).
Background: The limited space in the back of a JK means that you have to plan carefully. I've had a "shelf" across the back area that has been well used and nice to have. We throw all the light weight camping extras up there (chairs, tent when we take it, potty shelter, sun screen/shade, etc...mostly soft goods) and it has recently been the mounting point for a power inverter. It's useful and effective, BUT given that it's at a fixed height, mounting the new fridge below it will be a squeeze.
The Idea: Let's start over with the rear compartment design and go more modular/custom built with 80/20 extruded aluminum! What I am wanting to incorporate are the following: new Dometic fridge on a slide, the aux (house) battery, and create a new "shelf "over the fridge for use as described above. We use FrontRunner Wolf Pack boxes for other storage and want to continue with them as well, so ideally the space to the side of the fridge will accommodate them well, and hopefully 4 of them. Finally, and perhaps the kicker of the design is that I do use the under floor cubby and don't want to lose access to it if possible.
So, my thought is to create a "U" shape base if you will out of 1" 80/20 that would mount to the floor using the factory tie down points in the floor on the sides and across the back of the back seat. To this, I'd mount another second story level base that would hinge at the front so that if required I could get to the floor cubby, and that I can mount heavy duty drawer slides to for the fridge. That second tier if you will would be a full 4 sided affair with 1 additional fore/aft bar for the inside fridge slide. Getting the fridge tight to the driver's side rear with the hopes that the remaining space adjacent to the fridge could/would hold the 4 FrontRunner boxes up to appx the same overall height.......
I can then go vertical with the structure to "enclose" the fridge/create a space for the boxes/and then the "shelf" to support the camping stuff. Sounds simple, right? LOL
I hope my description makes sense, looking for advice on my theory, and any 80/20 specific thoughts or tips. Fire away with questions and thoughts and let's design this thing!
First, the vehicle: 2014 Jeep JK Unlimited (the 4 door for the non-Jeep crowd).
Background: The limited space in the back of a JK means that you have to plan carefully. I've had a "shelf" across the back area that has been well used and nice to have. We throw all the light weight camping extras up there (chairs, tent when we take it, potty shelter, sun screen/shade, etc...mostly soft goods) and it has recently been the mounting point for a power inverter. It's useful and effective, BUT given that it's at a fixed height, mounting the new fridge below it will be a squeeze.
The Idea: Let's start over with the rear compartment design and go more modular/custom built with 80/20 extruded aluminum! What I am wanting to incorporate are the following: new Dometic fridge on a slide, the aux (house) battery, and create a new "shelf "over the fridge for use as described above. We use FrontRunner Wolf Pack boxes for other storage and want to continue with them as well, so ideally the space to the side of the fridge will accommodate them well, and hopefully 4 of them. Finally, and perhaps the kicker of the design is that I do use the under floor cubby and don't want to lose access to it if possible.
So, my thought is to create a "U" shape base if you will out of 1" 80/20 that would mount to the floor using the factory tie down points in the floor on the sides and across the back of the back seat. To this, I'd mount another second story level base that would hinge at the front so that if required I could get to the floor cubby, and that I can mount heavy duty drawer slides to for the fridge. That second tier if you will would be a full 4 sided affair with 1 additional fore/aft bar for the inside fridge slide. Getting the fridge tight to the driver's side rear with the hopes that the remaining space adjacent to the fridge could/would hold the 4 FrontRunner boxes up to appx the same overall height.......
I can then go vertical with the structure to "enclose" the fridge/create a space for the boxes/and then the "shelf" to support the camping stuff. Sounds simple, right? LOL
I hope my description makes sense, looking for advice on my theory, and any 80/20 specific thoughts or tips. Fire away with questions and thoughts and let's design this thing!