Setting up to machine some aluminum d-ring hitch shackle mounts here in the shop. Going to send them out to be hard coat anodized when complete. I hate that everything out there is either powder coated or only type 2 anodized, which neither will hold up over time.
This is why I usually always end up making most of my own stuff.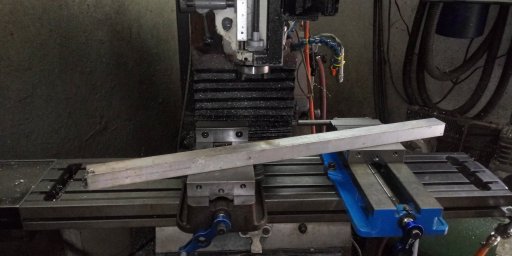
This is why I usually always end up making most of my own stuff.
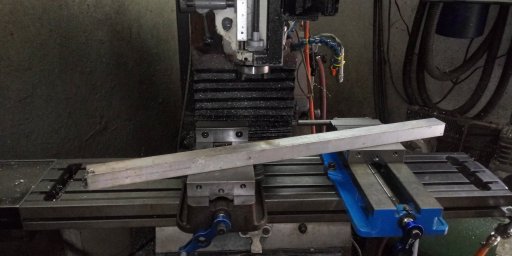