Rear fender trim update-
There is tons of write ups and how to videos out there on how to trim the rear fenders on a WJ and I think I watched all of them. They range from cutting with a sawzall and hammering the metal over to full on fender relocating with adding in new sheet metal, mine falls somewhere in the middle, but so far I'm happy with the result. For those of you that don't know the rear fender opening on the WJ consists of an inner and outer piece of sheet metal and the distance between the two varies depending on what part of the opening you're working on. So when you start to tackle this job in needs to be approached differently depending on the section you are working on. After watching and reading for a couple weeks on how to do this job I decided on the method of cutting, folding over, reattaching with body panel adhesive and covering with seam sealer.
Here is what I lined out to cut, the tape is 1/4" wide, I put it right on the edge of the door opening and then followed the shape of the original fender opening.
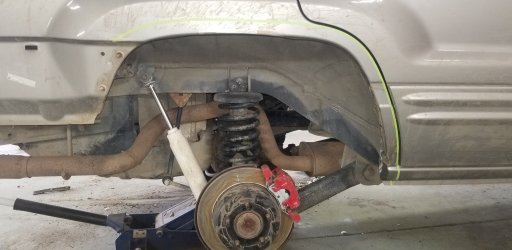
Next up was to start the cutting! My tool of choice was a die grinder with a 3" cut off wheel. First step was to separate the inner and outer pieces of sheet metal, to do this cut on the edge of the fender opening where it turns in 90 degrees to make the factory lip.
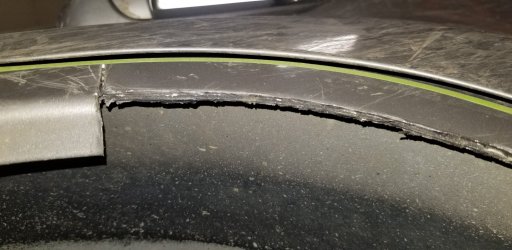
At this point you should be able to get a screwdriver in between the two pieces and open them up. I don't have any pics of it, but there is a bunch of foam insulation/ sound deadening in there that you want to scrape out as you go so you don't start a fire. When you're separating the sheet metal only take off enough of the lip to get them apart, you will need the extra length of the outer skin for folding over later. Now that they are apart you can move on to make the 100's of bend cuts, the closer together you make them the smoother the radius of the fender opening will be. In the areas where the opening had a tighter curve I tried for 1/4"-3/8". Cut just up to the tape and try to keep them as even as possible because if you are short of the tape on one and cut into the tape on the next it will show. At this point I'll cover how to do the front section, then the middle and rear as each area of the opening requires a little different approach.
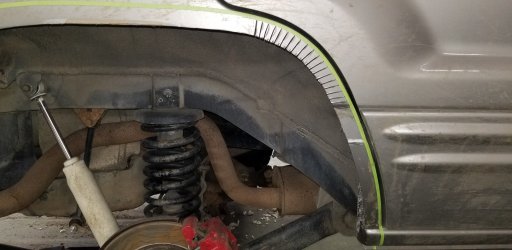
Once those are made you will remove a portion of the inner sheet metal using your bend cuts as a guide as to how much to cut out. Doing this make for less metal to bend but also creates a gap in some places.
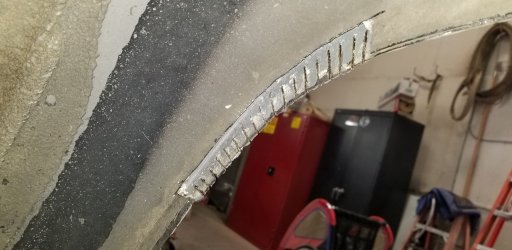
I wish I had taken more pictures at this point, but I fail you... But in the pic above you can see I went about 1/4" past my bend cuts, this was because at this part of the fender the inner piece of sheet metal had the start of a bend and cutting it out would allow for a better bend of the outer skin. Before I bent anything over I took a 3" 80 grit flap wheel on a 90 degree die grinder and cleaned things up to bare metal to help the panel adhesive stick. Once were cleaned up I took a flat nose punch and hammered in the inner sheet metal to close some of the gaps up, then began to bend over all the little tabs of the outer skin. You can use a pair of needle nose vise grips or just do it by hand. After they were all bent over for that section I worked it with a hammer, hitting right on the corner of the bend to get the bends to roll in tighter. Next just lightly tap the tabs down into place until they looked seated up to the inner piece of sheet metal. Once I was happy with how they were laying I came back with the die grinder and cut off any excess material, leaving about a 1/4" past the gap between pieces.
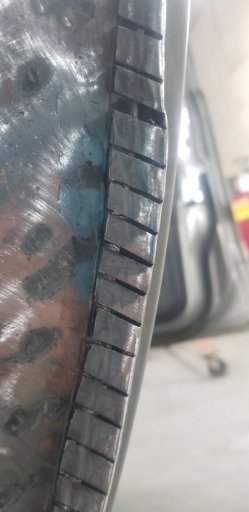
Now that the front radius of the opening was done I moved onto the rocker. Start with cutting off the end cap of the rocker and removing all the foam. After that it's pretty much the same process, but instead of removing the inner piece of sheet metal I bent it out towards the outer skin to close some of the gap and made the same type of bend cuts in the outer skin to fold it over the inner skin. Also just inside the rocker is a pinch weld that I just hammered over.
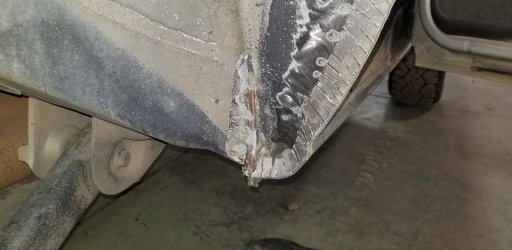
After that I mover on to the upper portion of the wheel open which is really the easiest part and can be bent up in three sections. Same process as before but at this section the 2 pieces of body panel are really close so you can just trim back the inner skin and fold the outer over 180. Once it was folded over I took a hammer and dolly to it to tighten up the bend. In the next 2 pictures you can see chipped paint hanging down, I tried to score it with a razor blade before bending it but I don't think it helped much.

The rear of the opening is a mix of the first 2 sections, it transitions from bending over 180 to having some gap. I first started with cutting the pinch weld loose at the top so I could get it bent over and out of the way. Then made some more bend cut so I could get them bent over at the start of the transition.
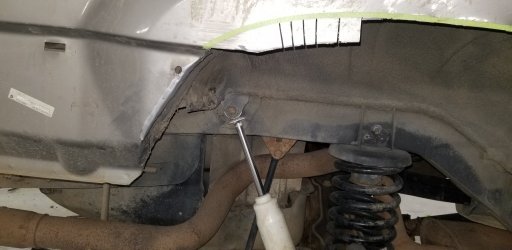
Once those were bent over it was the same process as doing the rocker: separate, bend inner skin out, outer skin in.
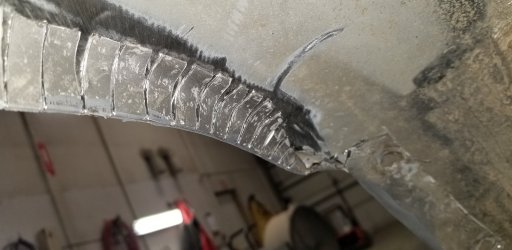
Once all the cutting, hammering and trimming was done I cleaned up the chipped paint a bit with the flap wheel and started in with the body panel adhesive. I've checked out a couple how to's on this job and seen where people used this instead of tacking things back together with results so I thought I would give it a go. I put it on pretty thick, got smoothed out and let it cure over night.
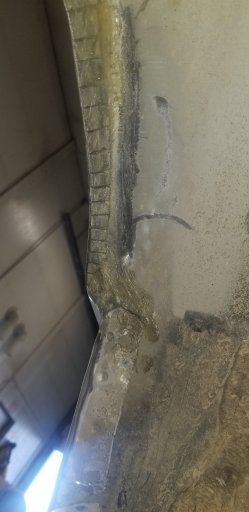
I followed the adhesive up with a coat of seam sealer to fill any pin holes and help smooth out any sharp edges I might have missed.
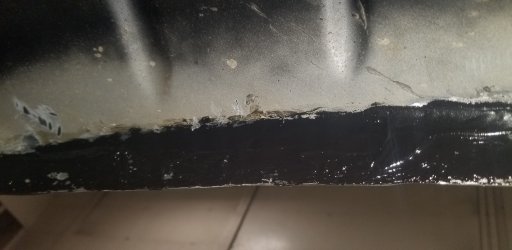
Once that dried I taped off the wheel opening and hit it with a coat of flat black paint. For the bumper trim I just used the cut off wheel and followed the line I made when I lined out the fender opening. I didn't add any new attachment points (I cut out a few with the trim) But I have a few hundred miles on it since I trimmed with no issues. Here is a pic with the trim job complete and the 33's. Next project will be adjustable upper and lower control arms in the front to be able to push the axle forward a bit, a set of 3/4" leveling spacers and quick disconnects. Parts should be here in the next week!