About a year ago I bough an old Ford Transit mk1 RV in pretty bad shape (turned out to be even worse than I expected) to refurbish. During disassembly I noticed it had a solid front axle, and it seemed feasible to put a front axle from a 4x4 on. I have always wanted a proper 4x4 camper van, so I went for it and got out the angle grinder. First I needed to cut out all the rust and remove the camper box, after I was finished not much was left of the car.
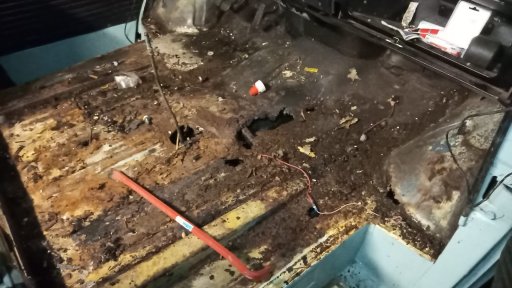
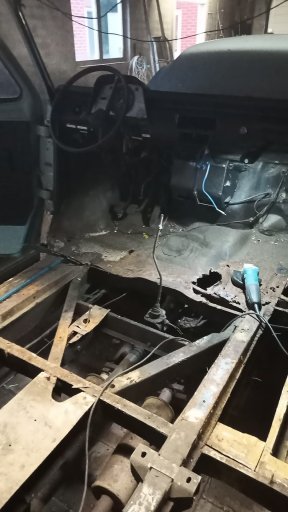
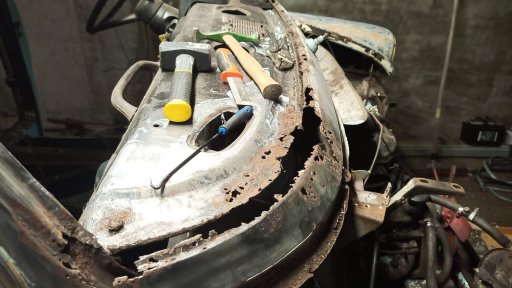
I found some second hand Land Rover Discovery 2 axles and an LT230 transfer case online, luckily without the land rover attached. To use the transfer case in the ford I will make it divorced from the original Ford gearbox, mounted in a subframe in between the chassis tubes. I am going to weld a propshaft flange to a FTC5090 ZF input shaft I purchased from Ashchroft to attach the gearbox to the transfer Case. Pay attention when you order stuff from Ashcroft, I received Britpart parts from them. Hope it will last, i may order some NOS gear from Ebay.
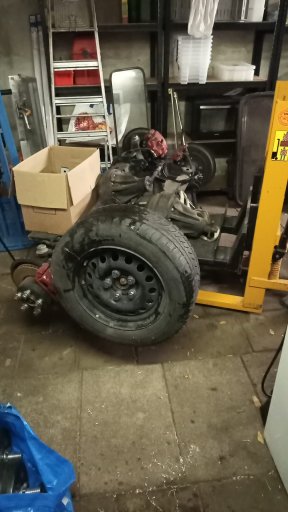
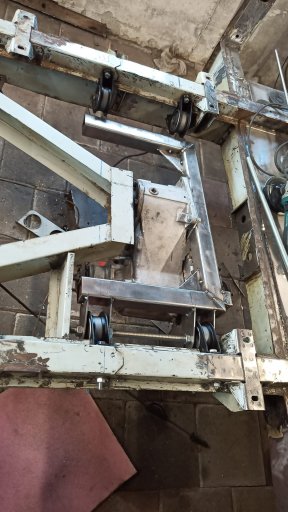
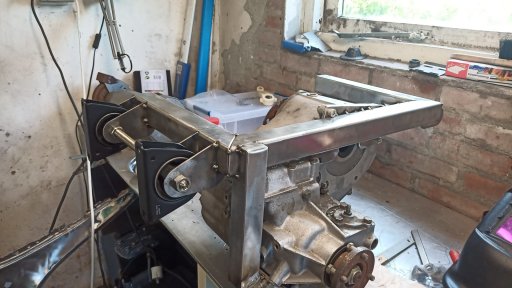
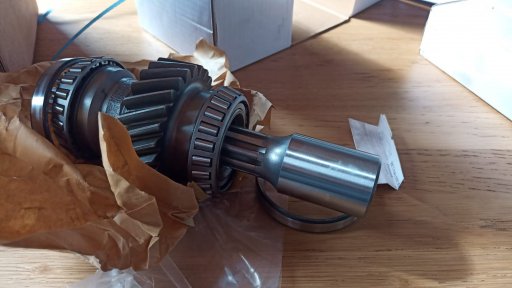
The Discovery 2 rear axle needed some mods in order to be used with leaf springs, I cut off the original mounting points and had some 6mm steel plate laser cut in the right shape.
The front axle needed less modification, with some cutting and grinding I managed to weld leaf spring mounting plates to the original attachment points.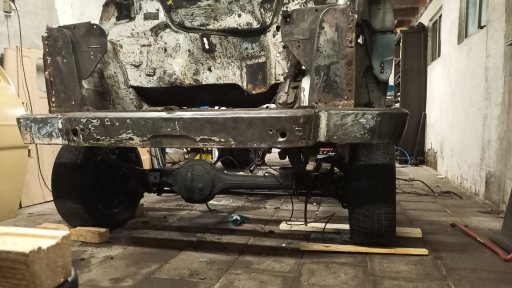
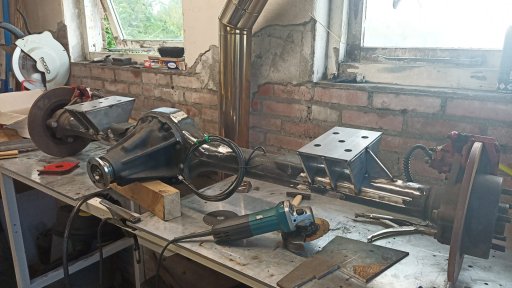
Tube sills as the original ones were completely rusted through, and I want to be able to put a high jack underneath
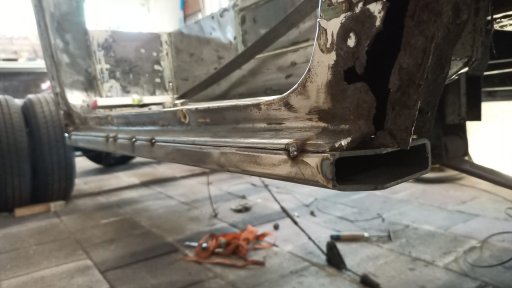
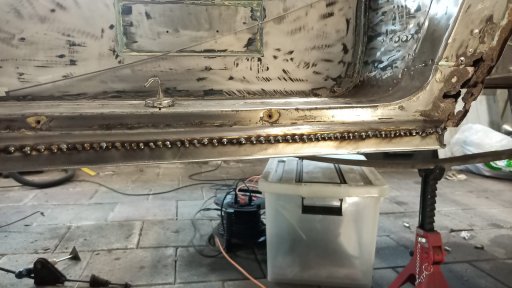
spent a lot of time cutting and welding in new pieces of sheet metal, but this week I finally came to the point of applying the first layer of primer and sealing all the welds and seams with seam sealant.
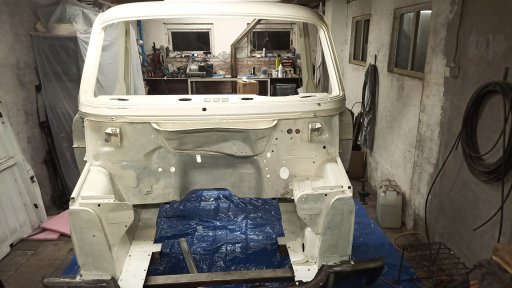
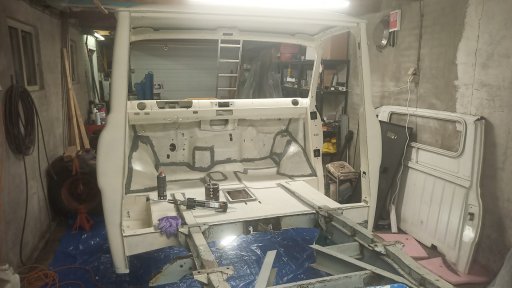
Still lots of work to be done, but the car looks a lot nicer now there's some paint on it.
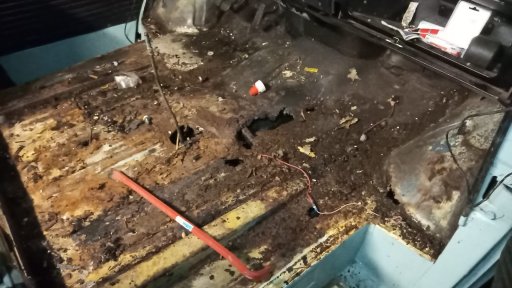
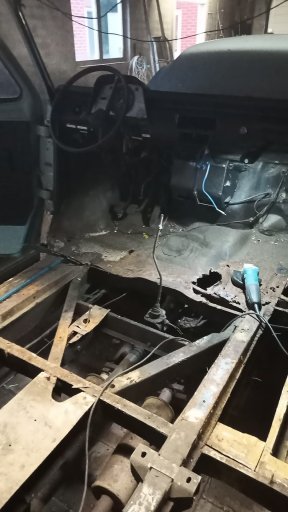
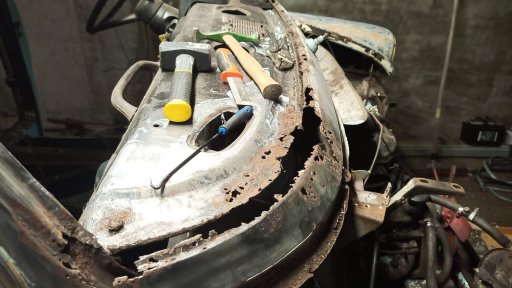
I found some second hand Land Rover Discovery 2 axles and an LT230 transfer case online, luckily without the land rover attached. To use the transfer case in the ford I will make it divorced from the original Ford gearbox, mounted in a subframe in between the chassis tubes. I am going to weld a propshaft flange to a FTC5090 ZF input shaft I purchased from Ashchroft to attach the gearbox to the transfer Case. Pay attention when you order stuff from Ashcroft, I received Britpart parts from them. Hope it will last, i may order some NOS gear from Ebay.
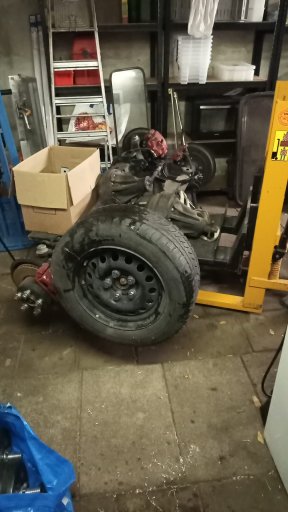
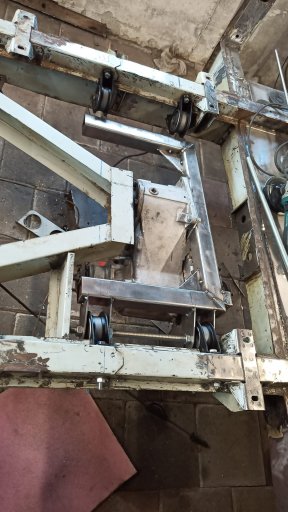
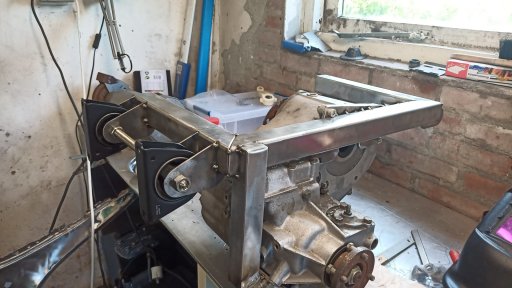
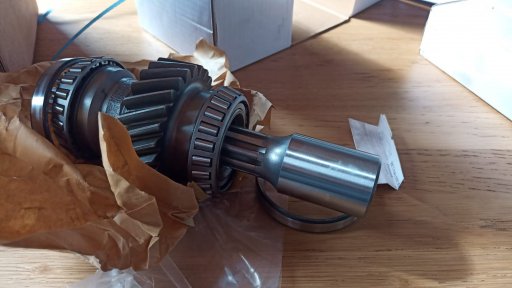
The Discovery 2 rear axle needed some mods in order to be used with leaf springs, I cut off the original mounting points and had some 6mm steel plate laser cut in the right shape.
The front axle needed less modification, with some cutting and grinding I managed to weld leaf spring mounting plates to the original attachment points.
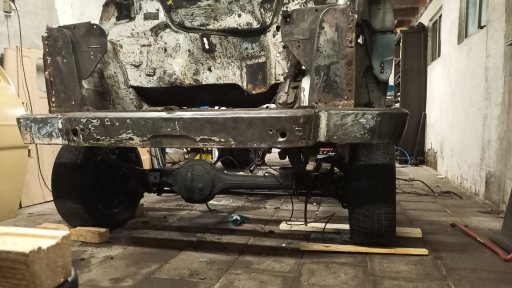
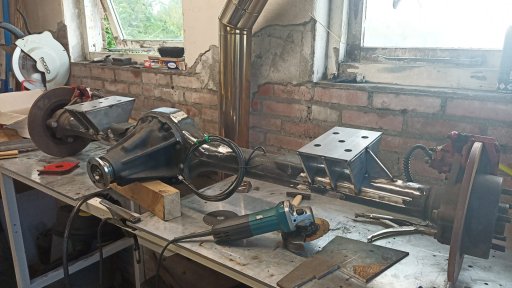
Tube sills as the original ones were completely rusted through, and I want to be able to put a high jack underneath
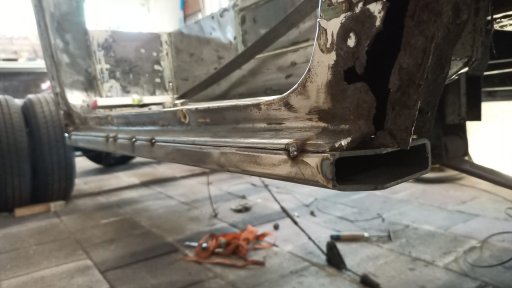
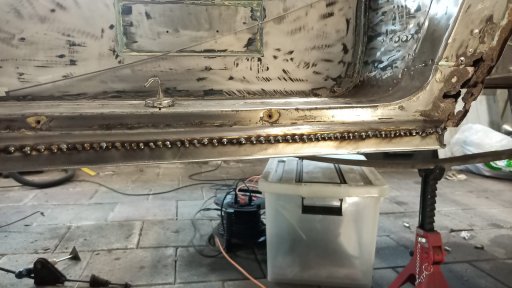
spent a lot of time cutting and welding in new pieces of sheet metal, but this week I finally came to the point of applying the first layer of primer and sealing all the welds and seams with seam sealant.
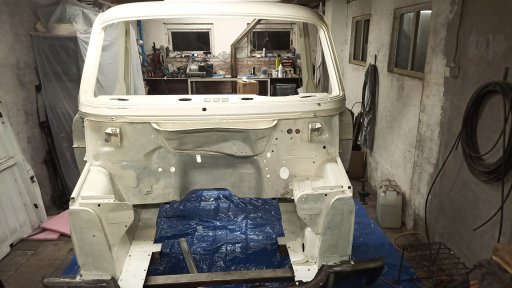
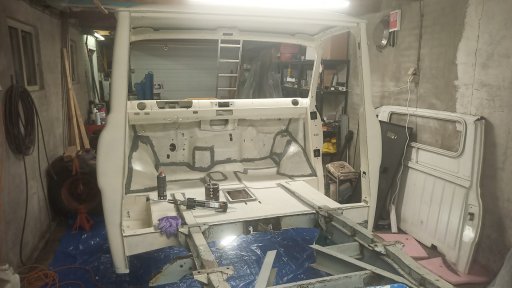
Still lots of work to be done, but the car looks a lot nicer now there's some paint on it.
Attachments
-
196.5 KB Views: 12
-
211.3 KB Views: 12
-
238.1 KB Views: 12
-
124 KB Views: 19
-
383.8 KB Views: 20
-
319.5 KB Views: 21
-
178.1 KB Views: 15
-
221.4 KB Views: 14
-
120.9 KB Views: 14
-
288.9 KB Views: 14
-
325.2 KB Views: 14
Last edited: